Troubleshooting the Monoprice Maker Select v2
A lot of troubleshooting questions asked about the Monoprice Maker Select v2 are centered around the same issues. Check out this page to view these issues and their most common solutions.
Let’s get started.
Under Extrusion/No Extrusion
When there’s an incorrect amount of plastic being extruded, no filament is coming out of the nozzle, or filament is “curling” out of the nozzle.
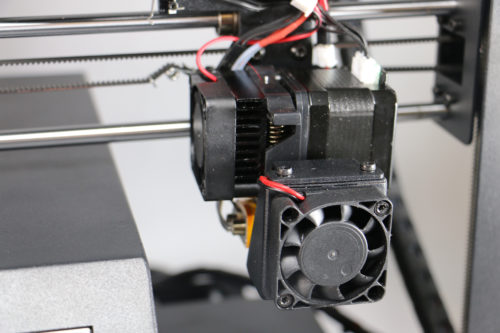
Issues with Heating and Temperature Regulation
“Heat Failure” codes are being received or your machine is not maintaining heat.
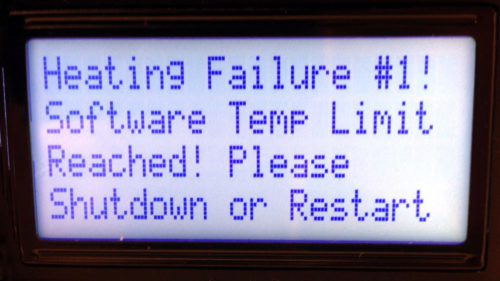
The Axis Does Not Move
There are a few causes that could lead to issues with the movement of the axis on your printer.
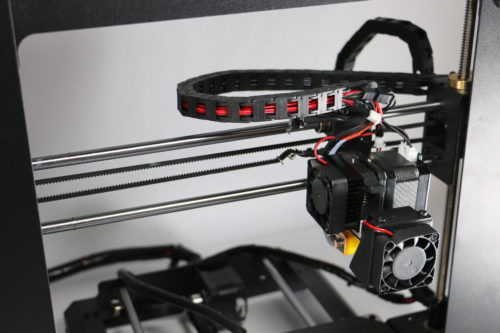
Stuttering/Step Skipping
You notice a stuttering at the same location of each layer, or your printer is shifting layers.
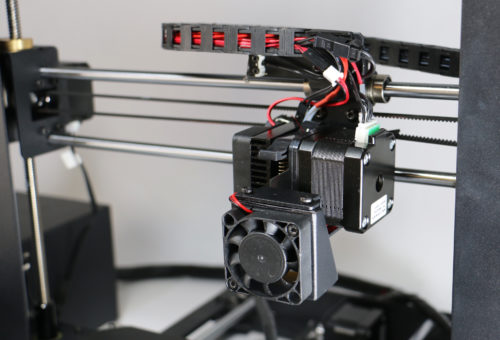
The LCD Screen or the SD Card is not Working
There are a few simple solutions if you’re noticing that your LCD screen isn’t lighting up or your SD Card isn’t reading.
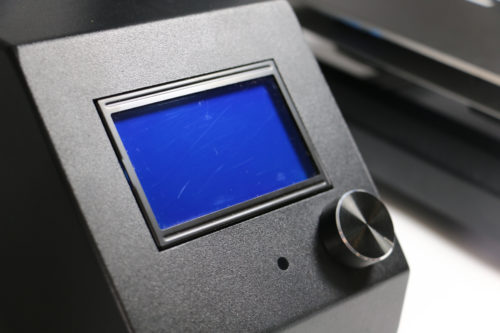
Axis Crashes
A few adjustments or a replacement may be needed if your axis is crashing.
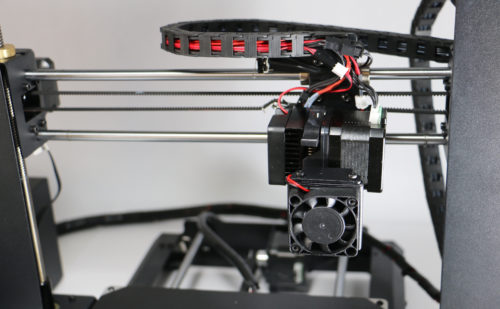
Extruder Stops Mid-Print
Your prints are failing part-way or about a half-hour into the printing process.
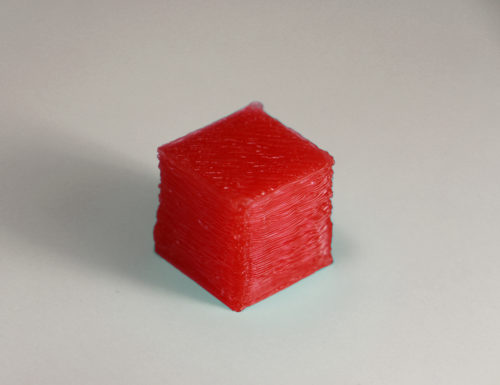
Stepper Motor Not Working
The stepper motors are not running or they are running but not operating.
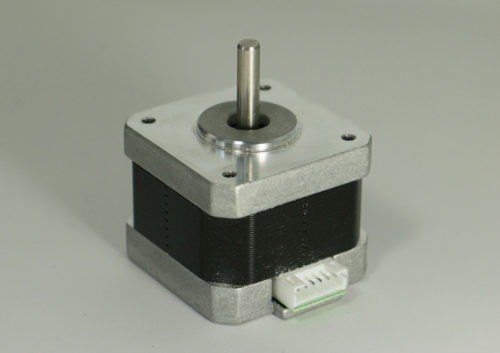
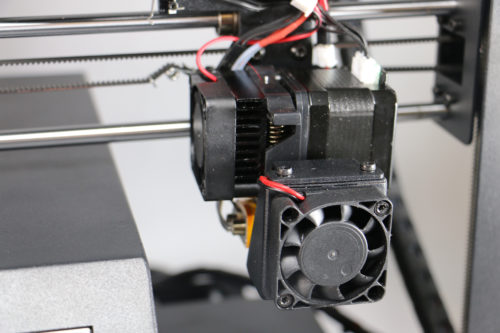
Under Extrusion/No Extrusion
The front fan may not be spinning, may be missing blades, spinning slowly, or mounted incorrectly. Visibly check to for any of these issues. Also check to ensure that the fan is getting 12 volts of power at max fan speed. If it is not, it is spinning slowly. The fan will need to be replaced or remounted.
A piece of filament may be stuck in the teeth of the hobbed gear. If this is the case, use a wire brush or toothpick to clean out the teeth. This gear may also be worn down and may need to be replaced.
Your heat sink may be mounted incorrectly. If the fins are facing in, towards the extruder assembly, then you will need to flip your heat sink.
There are several places that the filament path could clog. The thermal barrier tubing or the nozzle could be clogged. If you cannot easily unclog the hot end, you may need to replace part or all of your hot end.
You may be using filament that is of low quality or has irregularities in its shape. This can slow the flow of filament or can stop it altogether. Try using a different spool of filament and see if the problem is still present. You can also measure the amount of filament that is extruded with calipers to ensure that the stepper motor is extruding the correct amount. Fargo 3D Printing sells 3D-Fuel brand filament, whose quality we vouch for.
Your printer may be printing at a temperature that is too low for your filament. Try increasing the printing temp to the maximum temperature or above the recommended temperature range.
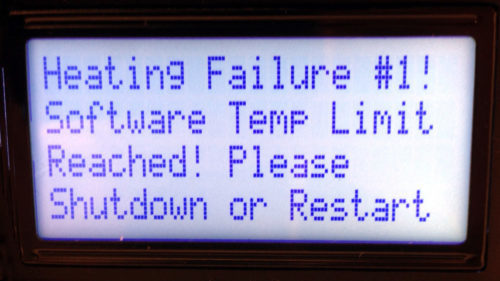
Issues with Heating and Temperature Regulation
Run a pre-heat. If your printer is not displaying that it is heating up, but you observe that the heater block is heating up, then the thermistor is most likely faulty. Check to make sure that the thermistor wire is not cut or damaged, then replace the thermistor.
Run a pre-heat. If the heater block does not heat up, then the heater cartridge is most likely faulty. Check to make sure the wire to the heater cartridge is not cut or damaged, then replace the cartridge.
PID settings control how much power is sent to the heater cartridge. Over time, these settings can change and may need to be reset.
Check the ceramic tape. If it is torn or missing it may be causing irregular heating or heat creep. If this is the case, replace the ceramic tape.
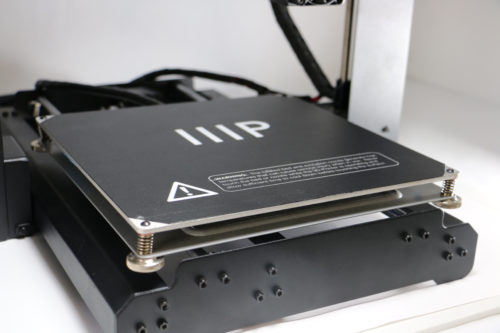
Bed Stopped Heating
The connectors from the print bed to the motherboard may have melted or may be charred. If this is the case, your printer may have smoked or started to smell before your print bed stopped heating. To check the connectors, open the electronics case and see if the connectors for the heated bed are melted or charred black. If so, your motherboard will need to be replaced.
To check the wiring, open the electronics case and make sure the wires for the print bed are plugged in and undamaged. If they are, check the resistance on these wires. If the wires are damaged or cut, they will need to be replaced.
To check the voltage to the print bed, open the electronics case and pre-heat the print bed. Use a volt meter to ensure that the bed is getting 12V. If it is, then either the wiring or the bed itself is faulty and will need to be replaced. If the bed is not getting 12V, then the motherboard is faulty and will need to be replaced.
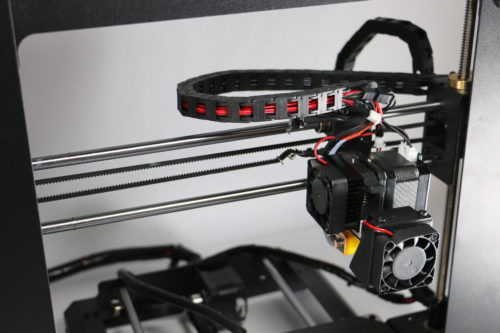
The Axis Does Not Move
The pulley may be worn. Check the pulley to see if it spins smoothly and check to ensure no teeth are missing. If the pulley is damaged or worn, replace the pulley.
Check the tightness of the belt. If it is too loose, the pulley may not turn the belt. In this case, tighten the belt.
Check the set screw on the pulley. If this is loose, the motor will spin without spinning the pulley. To fix, tighten the set screw.
Check Troubleshooting Chart for Stepper Motor Not Working.
Turn the axis by hand and observe if there are any rough spots. If so, find out why.
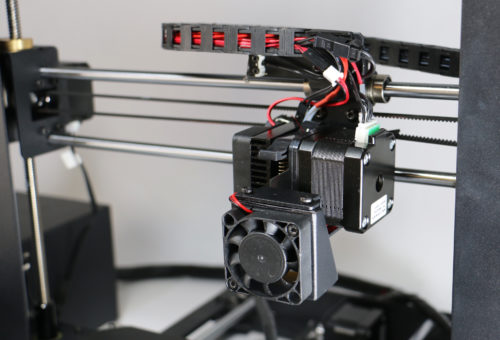
Stuttering/Step Skipping
Check all connections from the motherboard to the stepper motor to ensure they are not loose, cut, or damaged.
Turn the axis by hand and observe if there are any rough spots. If so, find out why.
Check the Troubleshooting Chart for Stepper Motor Not Working.
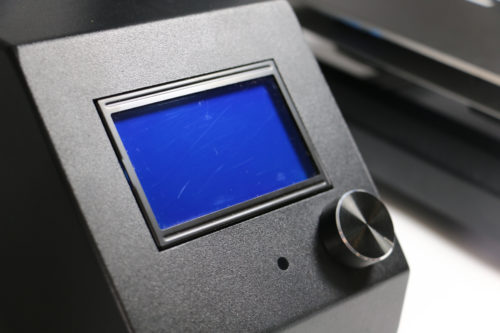
The LCD Screen or the SD Card is not Working
Replace the LCD screen.
Replace the LCD screen.
Replace the LCD screen.
Replace the motherboard.
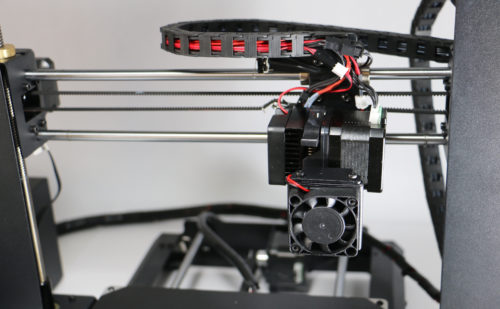
Axis Crashes
The end stop may be out of place or mounted incorrectly. Check the mount bracket to see if it is bent or missing screws. You may need to replace the bracket or remount it.
The end stop may be damaged. If so, replace.
Check the wires to the end stop to see if they are cut or damaged. Also check the resistance of the wires. If they are damaged or broken, replace the wires.
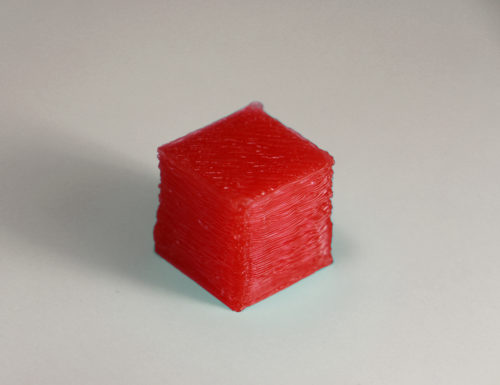
Extruder Stops Mid-Print
The front fan may not be spinning, may be missing blades, spinning slowly, or mounted incorrectly. Visibly check for any of these issues. Also check to ensure that the fan is getting 12 volts of power at max fan speed. If it is not, it is spinning slowly. The fan will need to be replaced or remounted.
Your fan spacer may be missing. If so, replace it.
Your heat sink may be mounted incorrectly. If the fins are facing in, towards the extruder assembly, then you will need to flip your heat sink.
The PTFE liner may be black or burnt. If this is the case, it needs to be replaced.
You may be using filament that is of low quality or has irregularities in its shape. This can slow the flow of filament or can stop it altogether. Try using a different spool of filament and see if the problem is still present. You can also measure the amount of filament that is extruded with calipers to ensure that the stepper motor is extruding the correct amount.
A piece of filament may be stuck in the teeth of the hobbed gear. If this is the case, use a wire brush or toothpick to clean out the teeth. This gear may also be worn down and may need to be replaced.
The hot end may suddenly drop in temperature. Watch your temperature to see if the temperature drops rapidly by twenty or more degrees or if it drops gradually. If the drop is quick, there may be faulty wiring, a faulty heater cartridge, or a faulty thermistor. To troubleshoot these problems, check the Troubleshooting Chart for Issues with Heating and Temperature Regulation. If the drop is gradual, then your parts fan may be spinning too fast or your ceramic insulation may be damaged or missing.
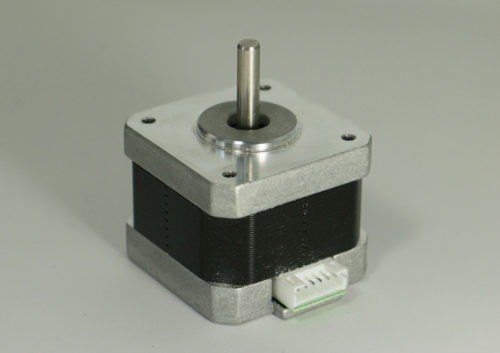
Stepper Motor Not Working
Check all connections from the motherboard to the stepper motor to ensure they are not loose, cut, or damaged.
Your stepper motor may be damaged or defunct. To check, unplug the stepper motor and plug it into an axis that you are sure works. If the motor still does not work, then it needs to be replaced.
First, check to ensure that the stepper motor works (previous step). If the motor works, then either the cable or the stepper driver is faulty. To check the cable, test the resistance on the wire leading to the motherboard. If the wire is damaged or cut, this cable will need to be replaced.
First, check to ensure that the stepper motor works and that the motor cable is not faulty (previous two steps). If the motor works and the cable is functioning, then the stepper motor driver is faulty, and your motherboard will need to be replaced.